Stainless steel plates are the backbone of industries from marine engineering to food processing, but choosing between 304 and 316 grades can make or break your project’s longevity. While 304 is the go-to for many applications, 316’s secret weapon—molybdenum—grants it unparalleled resistance in corrosive environments. Let’s dive into the science, data, and real-world performance to determine which grade truly reigns supreme.
Chemical Composition: The Core Difference
The key distinction lies in their alloy makeup:
Element | 304 (%) | 316 (%) | Role in Corrosion Resistance |
---|---|---|---|
Chromium | 18–20 | 16–18 | Forms passive oxide layer |
Nickel | 8–10.5 | 10–14 | Enhances ductility and stability |
Molybdenum | 0 | 2–3 | Combats chlorides and acidic pitting |
Carbon | ≤0.08 | ≤0.08 | Affects weldability and intergranular corrosion |
Why Molybdenum Matters:
This 2–3% addition in 316 dramatically improves resistance to:
- Chlorides (seawater, de-icing salts)
- Sulfuric acid
- Industrial solvents
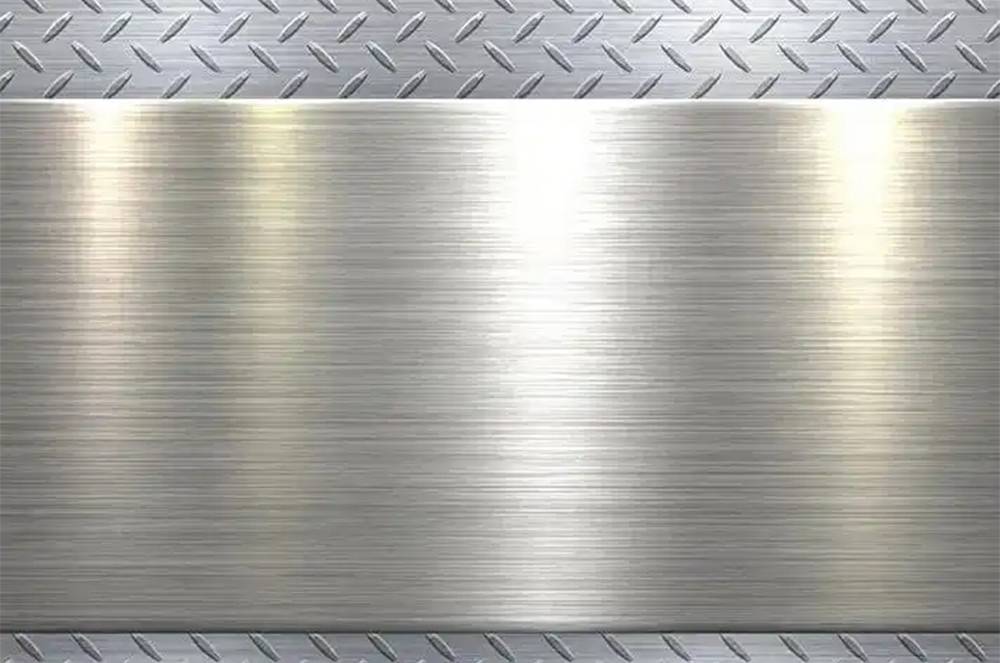
Corrosion Resistance Showdown
1. Pitting & Crevice Corrosion
- PREN (Pitting Resistance Equivalent Number):PREN=%Cr+3.3×%Mo+16×%NPREN=%Cr+3.3×%Mo+16×%N
- 304: PREN ≈ 19
- 316: PREN ≈ 26–33
- ASTM G48 Testing (Ferric Chloride):
- 304 fails at 25°C (77°F) within 24 hours
- 316 withstands up to 35°C (95°F)
2. Stress Corrosion Cracking (SCC)
- Chloride Threshold:
- 304: Fails at >50 ppm Cl⁻ (e.g., coastal air)
- 316: Tolerates up to 1,000 ppm Cl⁻ (e.g., chemical plants)
3. Uniform Corrosion
- Nitric Acid (65°C):
- Both grades perform similarly (<0.1 mm/year loss)
- Sulfuric Acid (10% concentration):
- 304: 0.5 mm/year loss
- 316: 0.1 mm/year loss
Real-World Applications: Where Each Grade Excels
Environment | 304 Performance | 316 Performance | Winner |
---|---|---|---|
Coastal Architecture | Moderate pitting in 5–7 yrs | No visible corrosion in 15+ yrs | 316 |
Food Processing | Excellent (non-acidic) | Overkill for most uses | 304 |
Chemical Tanks | High risk of SCC | Optimal for acids/chlorides | 316 |
Freshwater Pipelines | Cost-effective, durable | Unnecessary premium | 304 |
Case Study: A German offshore wind farm replaced 304 support plates with 316 after 3 years of severe pitting—extending service life by 12+ years despite higher upfront costs.
Cost vs. Durability: When to Invest in 316
- Price Difference: 316 costs 20–40% more than 304
- Break-Even Analysis:
- In marine environments: 316 lasts 3x longer → ROI within 4–6 years
- In mild indoor settings: 304’s lower cost prevails
5 Questions to Choose the Right Grade
- Chloride Exposure: Will the plates contact seawater, road salts, or bleach?
- Temperature: Operating above 60°C (140°F) accelerates chloride attacks.
- Budget: Can you justify 316’s premium for long-term savings?
- Aesthetics: Both grades look similar, but 316 retains finish longer in harsh conditions.
- Fabrication Needs: 316’s higher nickel improves weldability but requires specialized techniques.
Maintenance Tips to Maximize Lifespan
- For 304:
- Apply passivation (nitric acid) annually in humid climates
- Avoid chloride-rich cleaners
- For 316:
- Still requires rinsing after salt exposure
- Monitor for galvanic corrosion if paired with carbon steel
Future-Proofing Insight:
Emerging grades like 316L (low carbon) and 317L (higher molybdenum) offer even better corrosion resistance for extreme environments like pharmaceutical reactors or geothermal plants.
Conclusion
While 304 stainless steel plates suffice for general use, 316’s molybdenum-enhanced armor makes it the undisputed champion in corrosive environments. Prioritize 316 for:
- Marine applications
- Chemical processing
- Coastal infrastructure
Stick with 304 for:
- Indoor architectural panels
- Freshwater systems
- Budget-conscious projects