In the high-intensity world of welding, heat resistance isn’t just a benefit—it’s a necessity. Modern welding platforms now boast the ability to withstand sparks and temperatures reaching up to 1500°F every day. This breakthrough is revolutionizing how industrial welding operations are conducted by ensuring safety, durability, and reliability under extreme conditions.
Overcoming the Heat Challenge
Welding environments present constant challenges due to extreme heat and continuous spark exposure. Traditional platforms often fall short when faced with such high thermal stress, leading to increased maintenance costs and downtime. However, recent innovations in material science and engineering have enabled the development of welding platforms specifically designed to endure these demanding conditions.
The Breakthrough in Heat Resistance
Advanced welding platforms incorporate high-performance materials and engineered designs that dramatically improve heat tolerance. Key elements include:
- Innovative Materials: The use of refractory metals and specialized alloys that maintain structural integrity at high temperatures.
- Enhanced Cooling Systems: Built-in cooling mechanisms that dissipate heat efficiently, preventing damage during prolonged use.
- Optimized Design: Ergonomically designed surfaces that minimize heat accumulation while maximizing spark deflection.
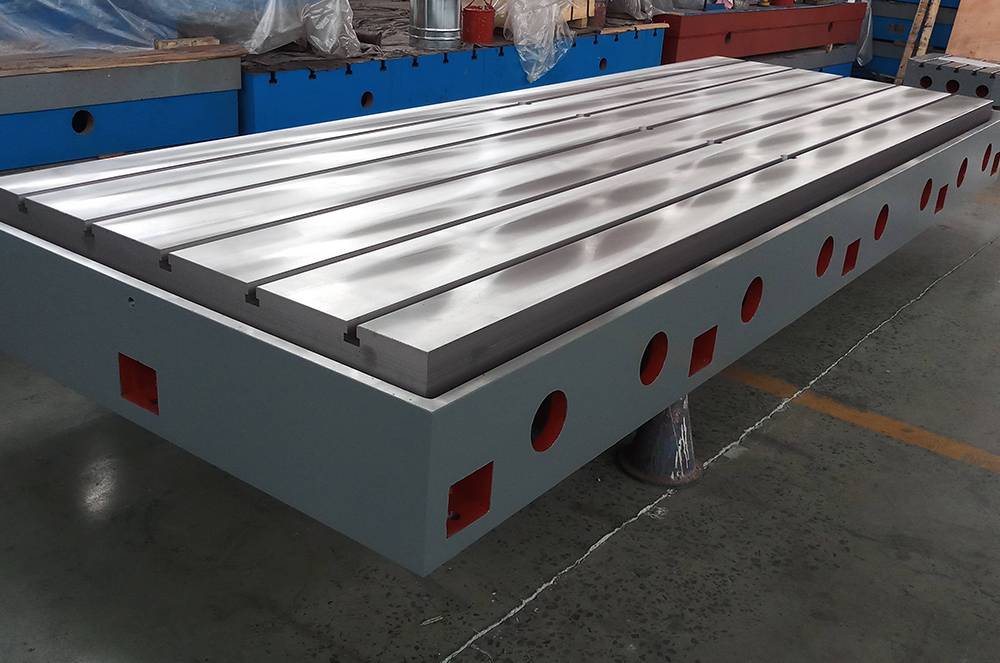
Key Features of Advanced Welding Platforms
The latest generation of heat-resistant welding platforms offers several notable features aimed at improving performance and safety:
Feature | Description | Benefit |
---|---|---|
High-Temperature Alloys | Engineered materials that retain strength and resist deformation at 1500°F | Ensures longevity and operational stability |
Integrated Cooling Systems | Innovative cooling channels that quickly dissipate heat generated by welding sparks | Reduces risk of overheating and damage |
Spark Deflection Design | Surface design optimized to redirect sparks away from critical components | Enhances safety and minimizes wear |
Maintenance Efficiency | Low-maintenance construction materials and design elements | Reduces downtime and operational costs |
Enhancing Safety and Efficiency
Welding platforms that can resist 1500°F sparks daily not only extend the lifespan of the equipment but also significantly enhance workplace safety. With reduced risk of thermal degradation, operators can focus on improving productivity without constant concerns about equipment failure. These platforms are engineered to meet rigorous industry standards, making them a reliable choice for modern industrial applications.
Future Directions in Heat-Resistant Welding Technology
The rapid advancement in material technologies and engineering techniques is paving the way for even more robust welding platforms. Future innovations may include smart monitoring systems that continuously assess temperature levels and predict maintenance needs, further reducing downtime and boosting overall productivity.
Conclusion
The breakthrough in heat resistance for welding platforms marks a significant step forward in industrial welding technology. By effectively withstanding 1500°F sparks daily, these platforms not only provide enhanced safety and durability but also offer a competitive edge to operations that demand high performance under extreme conditions. As the industry continues to evolve, investing in advanced, heat-resistant welding solutions will be key to maintaining operational efficiency and achieving long-term success.
Embrace the future of welding with platforms designed to thrive under intense heat and deliver unparalleled performance—ensuring your operations run smoothly, safely, and efficiently every day.