Avoid costly mistakes! Learn how to select stainless steel flanges for your piping system—explore material grades, pressure ratings, surface finishes, and compliance standards.
Stainless steel flanges are the backbone of industrial piping systems, ensuring leak-proof connections in everything from chemical plants to breweries. Yet, choosing the wrong flange can lead to catastrophic failures—one refinery paid $2.3 million in downtime due to a mismatched flange. Let’s break down the critical factors for selecting the perfect stainless steel flange for your application.
1. Material Grade Selection
Not all stainless steel is created equal. Match the alloy to your operating environment:
Grade | Key Properties | Best For | Avoid In |
---|---|---|---|
304 | Cost-effective, general corrosion resistance | Food processing, water systems | Chloride-rich or acidic environments |
316 | Molybdenum-enhanced resistance | Marine, chemical, and oil & gas | High-temperature sulfuric acid |
316L | Low carbon, weld-friendly | Pharmaceutical, cryogenic | Abrasive slurry flows |
Case Study: A German chemical plant reduced flange replacements by 80% after switching from 304 to 316L for their HCl vapor lines.
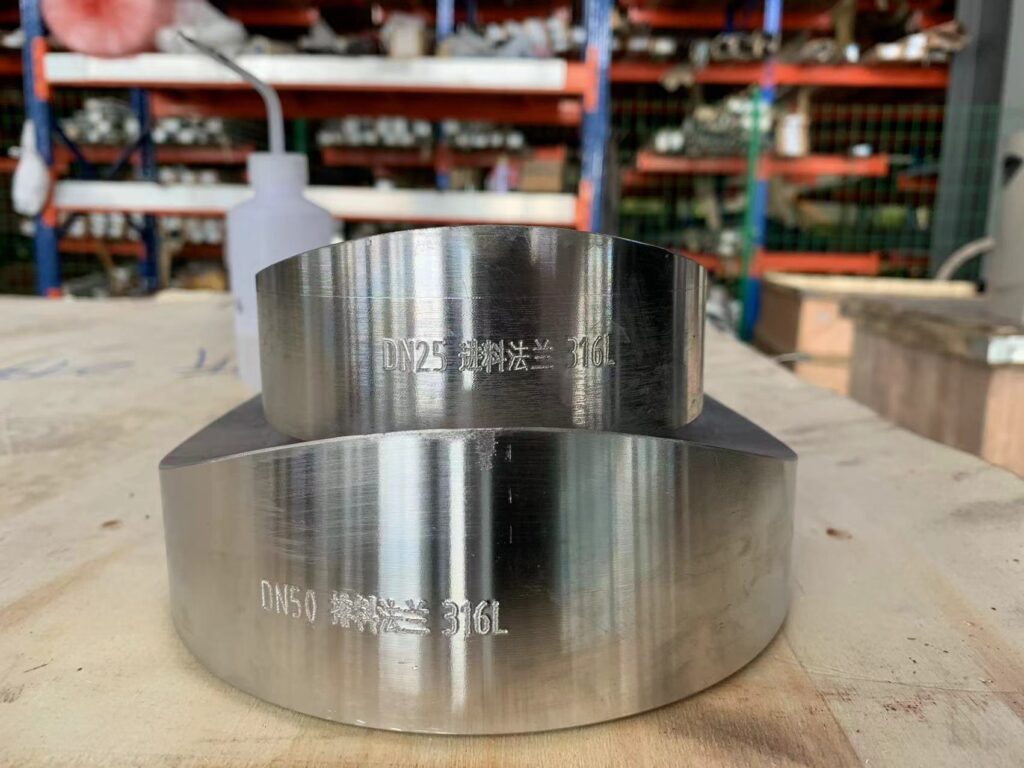
2. Pressure Rating Compliance
Flanges must withstand both internal pressure and external forces. Key standards:
- ASME B16.5: Class 150 to Class 2500 (PSI ratings)
- PN System: PN6 to PN100 (metric pressure classes)
Critical Rule: Always choose a flange rated for 20% higher pressure than your system’s maximum operating pressure.
3. Flange Face Type
The sealing surface determines leak prevention:
Face Type | Surface Finish (Ra) | Applications |
---|---|---|
Raised Face (RF) | 3.2–6.3 μm | Oil/gas, steam systems |
Flat Face (FF) | 6.3–12.5 μm | Low-pressure water lines |
Ring Joint (RTJ) | 0.8–1.6 μm | High-pressure (Class 900+) |
Pro Tip: Use RTJ flanges with spiral-wound gaskets for hydrogen service above 500°C.
4. Temperature Resilience
Stainless steel weakens at extreme temperatures:
- 304/316: Safe up to 870°C (intermittent)
- 310S: Handles 1,100°C (furnace flanges)
- Duplex 2205: Performs at -50°C (cryogenic LNG)
Always account for thermal expansion—calculate bolt stress using:σ=E⋅α⋅ΔT1−νσ=1−νE⋅α⋅ΔT
Where EE = Young’s modulus, αα = thermal expansion coefficient, νν = Poisson’s ratio.
5. Surface Finish & Coating
Prevent corrosion and contamination:
- Electropolishing: Achieves Ra 0.4 μm for pharma-grade systems
- Pickling: Removes iron contamination (critical for semiconductor fabs)
- Xylan Coating: Reduces friction in high-velocity gas pipelines
6. Certification & Traceability
Demand these documents:
- Mill Test Certificate (MTC) with heat number
- NACE MR0175 for sour gas (H₂S) environments
- PED 2014/68/EU for European pressure equipment
Red Flag: Suppliers offering “equivalent” grades without proper certifications often cut corners.
7. Cost vs. Lifetime Value
While cheaper flanges may save 30% upfront, consider:
- Maintenance Costs: A single leak repair can cost 5x the flange price
- Downtime Impact: Unplanned shutdowns average $10k/hour in manufacturing
- Replacement Cycle: Premium 316L lasts 3x longer than 304 in coastal areas
Common Mistakes to Avoid
- Mixing Standards: ASME vs. DIN flanges have different bolt hole patterns
- Ignoring Gasket Compatibility: PTFE eats into 304 stainless at >200°C
- Over-Torquing Bolts: Exceeding 75% of yield strength causes stress cracking
Maintenance Checklist
- Monthly: Inspect for pitting corrosion with a 10x magnifier
- Annually: Hydro-test at 1.5x operating pressure
- Every 5 Years: Replace gaskets and recalibrate bolt tension
Future-Proofing Tip:
Look for flanges with Smart Sensor Ports—embedded IoT devices that monitor real-time stress and temperature, predicting failures 6–8 months in advance.
Conclusion
Choosing the right stainless steel flange requires balancing material science, mechanical engineering, and operational economics. By following this 7-step framework, engineers can reduce failure risks by 90% while optimizing total cost of ownership.