Stainless steel is renowned for its corrosion resistance and aesthetic appeal. However, even these resilient materials can succumb to corrosion if not properly maintained. In this post, we’ll explore several strategies to prevent corrosion in stainless steel components, ensuring they remain durable and functional over time.
Understanding Corrosion in Stainless Steel
Despite its protective chromium oxide layer, stainless steel can corrode under certain conditions. Factors such as harsh environments, improper cleaning, or damage to the protective film can compromise its integrity. Understanding these vulnerabilities is the first step in effective corrosion prevention.
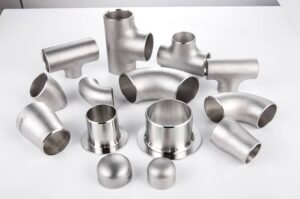
Key Strategies for Corrosion Prevention
Several methods can enhance the longevity of stainless steel components by preventing corrosion. Here are some key strategies:
1. Regular Cleaning and Maintenance
- Routine Inspections: Regular checks help identify early signs of corrosion.
- Appropriate Cleaning Agents: Use non-abrasive cleaners that do not damage the passive layer.
2. Passivation Treatments
- Enhancing the Protective Layer: Chemical passivation treatments can restore and strengthen the chromium oxide film.
- Post-Fabrication Treatments: Apply passivation soon after fabrication to ensure maximum protection.
3. Environmental Control
- Control Humidity: Reducing moisture in the environment can prevent the onset of corrosion.
- Avoid Chloride Exposure: Chlorides can break down the passive layer, so minimizing exposure is crucial.
4. Proper Alloy Selection
- Match Material to Environment: Certain stainless steel grades are more suitable for corrosive environments. Selecting the right alloy minimizes risk.
- Consider Coatings: In extreme conditions, additional protective coatings may be applied to further shield the component.
5. Design Considerations
- Avoid Crevices and Gaps: Design components to minimize areas where corrosive agents can accumulate.
- Ensure Proper Drainage: Prevent water accumulation by incorporating efficient drainage features.
Comparison of Corrosion Prevention Techniques
Below is a table summarizing various prevention methods and their benefits:
Prevention Method | Benefits | Key Considerations |
---|---|---|
Regular Cleaning | Removes contaminants; maintains protective layer | Use mild, non-abrasive cleaning agents |
Passivation | Restores and strengthens the chromium oxide film | Best applied post-fabrication |
Environmental Control | Reduces exposure to corrosive agents like moisture and chlorides | Implement dehumidifiers; control indoor conditions |
Alloy Selection | Matches material properties to environmental demands | Choose alloys based on specific exposure risks |
Design Optimization | Minimizes areas where corrosion can initiate | Avoid crevices; ensure proper water drainage |
Best Practices for Long-Term Durability
- Establish a Maintenance Schedule: Create a routine maintenance plan that includes cleaning, inspections, and passivation treatments as needed.
- Educate Your Team: Ensure that everyone involved in handling and maintaining stainless steel components understands best practices for corrosion prevention.
- Monitor Environmental Conditions: Regularly assess the surrounding environment and take steps to mitigate any factors that could contribute to corrosion.
Conclusion
Preventing corrosion in stainless steel components is achievable through a combination of proper material selection, regular maintenance, and smart design choices. By adopting these strategies, you can extend the life of your stainless steel products and ensure they perform optimally in even the most challenging environments. Whether you are in manufacturing, construction, or any industry where stainless steel is integral, these prevention methods can help maintain the integrity and functionality of your components.
Taking proactive steps today will not only protect your investment but also enhance customer satisfaction by delivering reliable, high-quality products that stand the test of time.