With the rapid development of the industrial manufacturing sector, stainless steel pipes have become a crucial material in many engineering projects due to their excellent corrosion resistance and strength. However, in recent years, the issue of wrinkles appearing on the surface of stainless steel pipes has garnered widespread attention within the industry. While these wrinkles may seem to only affect the pipe’s appearance, they can also have negative impacts on the structural integrity of the pipe.
Understanding the causes of these wrinkles is essential for improving production efficiency and ensuring product quality. Today, we will explore the various factors that contribute to this phenomenon, helping readers grasp the scientific principles behind the wrinkling of stainless steel pipes.
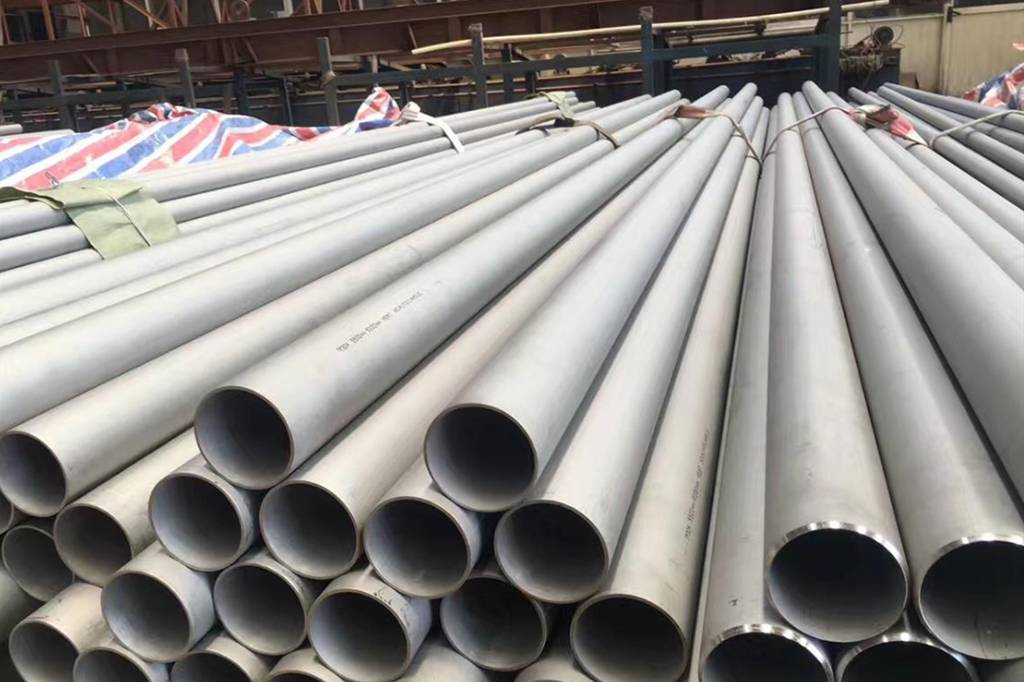
Main Causes of Wrinkles in Stainless Steel Pipes
- Stress During the Manufacturing Process
During the production of stainless steel pipes, processes like bending, forming, and welding subject the pipes to significant mechanical stress. If this stress is not properly managed, uneven forces may cause the surface of the pipes to deform, leading to wrinkles. This is especially common during forming and bending, as internal stresses in the metal are released, directly affecting surface smoothness. - Inadequate Lubrication
Lubrication plays a critical role when bending or forming stainless steel pipes. Proper lubrication reduces friction and ensures a smoother forming process. If insufficient lubrication is used, the surface of the pipe may experience higher friction, increasing the likelihood of wrinkles. - Temperature Fluctuations
Significant temperature changes during production are another important factor. For example, during heat treatment or welding, if temperature control is inadequate, localized heating or rapid cooling can cause uneven thermal expansion or contraction in the stainless steel, resulting in wrinkles. Precise temperature management is essential to maintaining the material’s stability. - Material Thickness
The thickness of stainless steel pipe material is also a key factor contributing to wrinkling. Thinner materials are more prone to deformation during bending or forming, making it harder for the surface to stay smooth under pressure. Strict control of material thickness during production is crucial to avoid unnecessary wrinkles. - Tooling and Equipment Issues
The quality of molds and tooling also directly affects production outcomes. If the molds are poorly designed or the equipment is heavily worn, the pressure applied during forming may be uneven, causing wrinkles to form on the pipe’s surface. High-quality tools and molds are fundamental to ensuring smooth production. - Welding Stress
During the welding process, especially when improper welding techniques are used, stress concentrations can occur at the weld joints. These stress concentrations can lead to localized deformation, causing wrinkles to appear near the welded areas. Using proper welding methods can effectively reduce the occurrence of this problem.
How to Address Wrinkling in Stainless Steel Pipes
For manufacturers of stainless steel pipes, addressing the issue of wrinkling is not just about enhancing the product’s appearance but also about ensuring the overall performance and longevity of the pipes. To tackle this, manufacturers can optimize their production processes, improve mold quality, enhance temperature control, and ensure adequate lubrication management. Additionally, industry professionals should receive proper training in welding techniques to ensure that each step of the process meets required standards.
With technological advancements, the manufacturing processes for stainless steel pipes will continue to improve, and the issue of wrinkling is expected to be further minimized. Understanding and mastering these contributing factors will help manufacturers optimize production workflows and provide higher-quality pipe products for various industries.