Stainless steel is a popular material known for its corrosion resistance, durability, and aesthetic appeal. It is widely used in various industries, including automotive, aerospace, medical, and food processing. However, to enhance its corrosion resistance further and ensure longevity, stainless steel often undergoes a process known as passivation. This article will explore the stainless steel surface passivation process flow, its benefits, and the science behind it.
What is Passivation?
Passivation is a chemical treatment process used to enhance the natural corrosion resistance of stainless steel. Even though stainless steel is inherently resistant to rust and corrosion due to the presence of chromium, which forms a thin, protective oxide layer on the surface, the metal can still be susceptible to corrosion under certain conditions. This can occur when contaminants, such as iron particles or other impurities, are present on the steel’s surface. The passivation process helps remove these contaminants and fortifies the protective oxide layer, ensuring that the stainless steel remains corrosion-resistant over time.
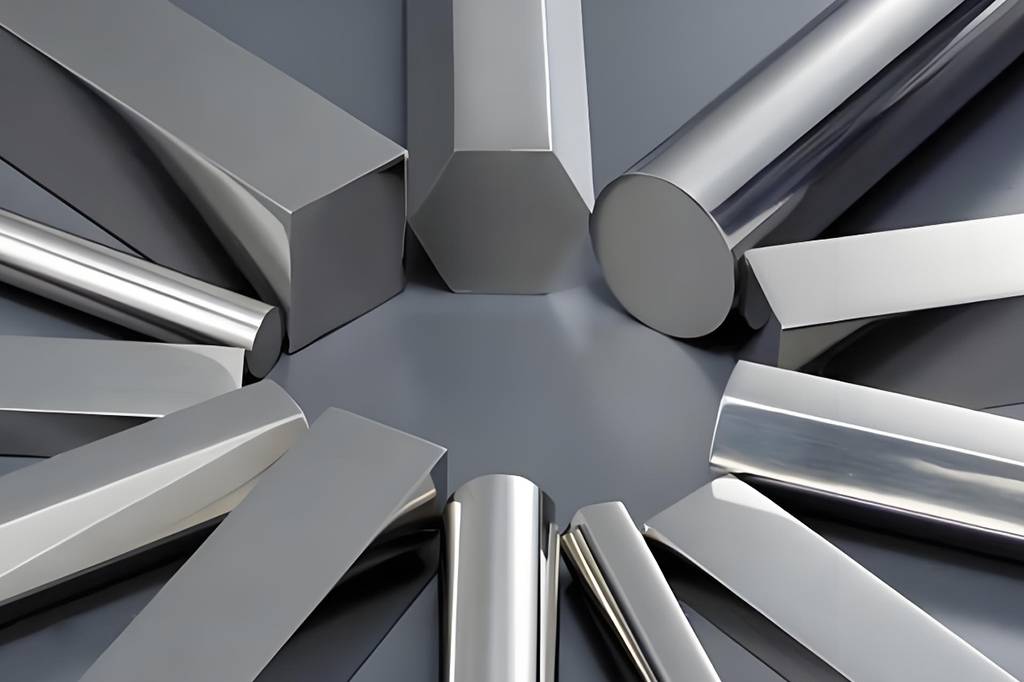
The Passivation Process Flow
The passivation process involves several key steps to ensure that the stainless steel surface is clean and protected. Here is an overview of the typical passivation process flow:
- Cleaning the Surface: The first step in the passivation process is thoroughly cleaning the stainless steel surface to remove any dirt, grease, oil, or other contaminants. This is usually done using alkaline cleaners or detergents that effectively remove organic residues. Proper cleaning is crucial, as any remaining contaminants can interfere with the passivation process and reduce its effectiveness.
- Rinsing: After cleaning, the stainless steel is rinsed with deionized water to remove any cleaning agents and loose particles. This step ensures that the surface is free of any residues that could negatively impact the passivation process.
- Acid Treatment: The cleaned and rinsed stainless steel is then immersed in an acid bath. Common acids used for passivation include nitric acid and citric acid. The acid bath serves two main purposes: it removes any remaining iron particles or other contaminants from the surface, and it helps form a new, thicker oxide layer. The choice of acid and the concentration used depends on the type of stainless steel and the desired level of passivation.
- Neutralization: After the acid treatment, the stainless steel is often rinsed again to remove any remaining acid. In some cases, a neutralizing agent, such as a mild alkaline solution, is used to neutralize the acid and ensure that no residues remain on the surface.
- Final Rinsing and Drying: The final step in the passivation process is thoroughly rinsing the stainless steel with deionized water to ensure that all chemicals are removed. The stainless steel is then dried, typically using hot air or a drying oven. Proper drying is important to prevent any water spots or other marks from forming on the surface.
Benefits of Passivation
The passivation process offers several benefits that make it an essential treatment for stainless steel in various applications:
- Enhanced Corrosion Resistance: By removing surface contaminants and forming a thicker, more stable oxide layer, passivation significantly improves the corrosion resistance of stainless steel, especially in harsh environments.
- Improved Cleanliness: Passivated stainless steel surfaces are less likely to harbor bacteria, making them ideal for applications in the medical, pharmaceutical, and food processing industries.
- Extended Lifespan: Passivating stainless steel helps extend its lifespan by reducing the likelihood of corrosion-related damage, thereby maintaining its appearance and structural integrity over time.